Award-Winning Biosolids Facility Provides Innovative Solution for Wastewater Byproducts
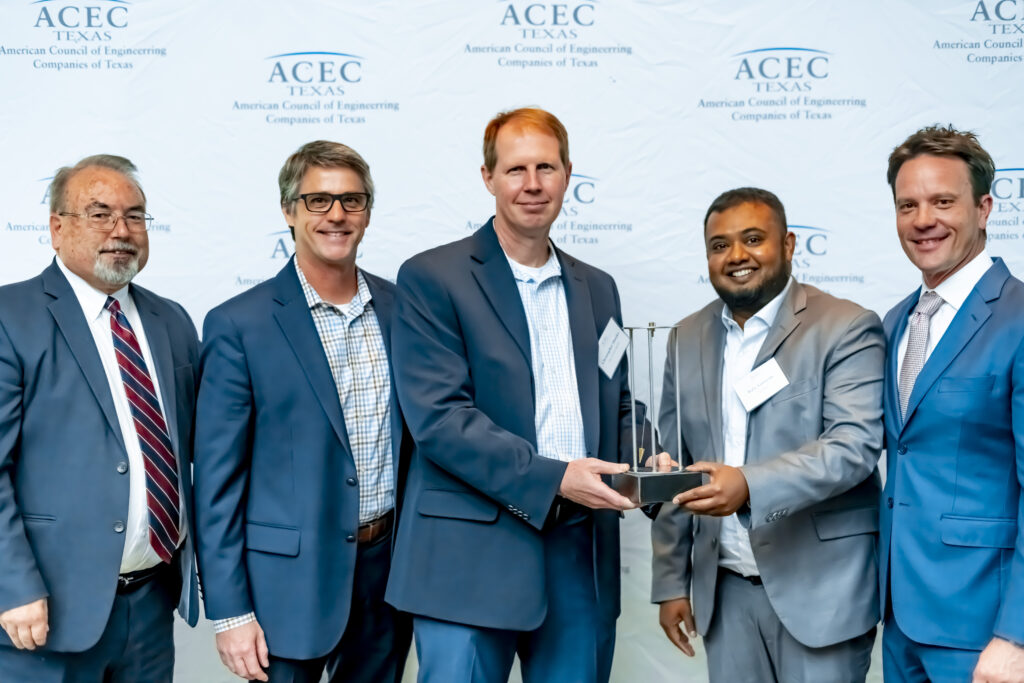
The City of Fort Worth’s commitment to promoting the beneficial and sustainable use of biosolids while using cost-effective and environmentally acceptable management practices continues at its new Village Creek Water Reclamation Facility (WRF) Biosolids Processing Facility. This $59 million project has several “first of its kind” innovative aspects, including the largest rotary drum dryer in the world in a biosolids application, a condensate water recycling system, and a nitrogen generation system that that increases the safety of facility. It provides an innovative and sustainable solution for thermally drying biosolids by replacing the existing belt filter presses/lime stabilization process with a centrifuge dewatering and drum drying process.
The project received the Gold Medal for Water and Wastewater in the ACEC Texas 2023 Engineering Excellence Awards and the 2023 Ronald B. Sieger Biosolids Management Award from the Water Environment Association of Texas.
Understanding Biosolids
Simply put, biosolids are the nutrient-rich byproduct of wastewater treatment processes that separate liquids from solids and in which the solids undergo further treatment for stabilization that meet state and federal requirements. They contain essential plant nutrients and organic matter that can be beneficially reused. The Village Creek WRF biosolids end product is a dry granulated pellet that is environmentally safe, 100 percent beneficially reused, and has multiple market outlets including use as a fertilizer, soil amendment, or use as a biofuel.
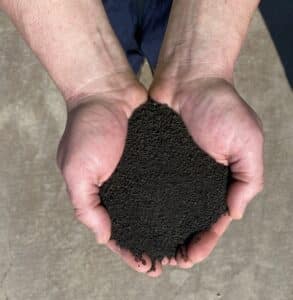
Collaborative Project Delivery for an Accelerated Schedule
Due to odor complaints at biosolids land application sites and increased overall biosolids program costs, the City needed to change how it processed biosolids. To meet this challenge, the City commissioned the development of a biosolids master plan to evaluate options. Based on on-site visits to understand the various options available and recommendations from the master plan, the City implemented direct thermal drying with a design-build-operate-maintain (DBOM) project delivery method. The City set an accelerated 30-month design-build schedule to implement the project, and the DBOM delivery method assisted in facilitating that schedule.
This was the first time the City had used the DBOM delivery approach, which allowed for collaboration throughout the design and construction phases between the City and the project team, which consisted of prime/long-term operator (Synagro), equipment designer-fabricator-supplier (Andritz), the balance of plant designer (Freese and Nichols), and the builder (Archer Western).
Synagro provided invaluable input based on their experience operating and maintaining drying facilities across North America. Long lead equipment and critical path construction items were identified early by Andritz and Archer Western so that the design and procurement of those items could be fast-tracked. FNI’s established working relationship with the City and intimate familiarity with the Village Creek WRF provided the cohesive force to keep the team on track and the project fully integrated with the plant’s existing infrastructure. The DBOM delivery approach reduced the project schedule by 18 months, saving the City roughly $4 million.
Innovative Solutions
Of the more than 16,000 municipal wastewater treatment plants in the United States, only about 100 plants thermally dry biosolids. The Village Creek WRF is the third thermal drying facility in Texas. Some unique and innovative aspects of this project are:
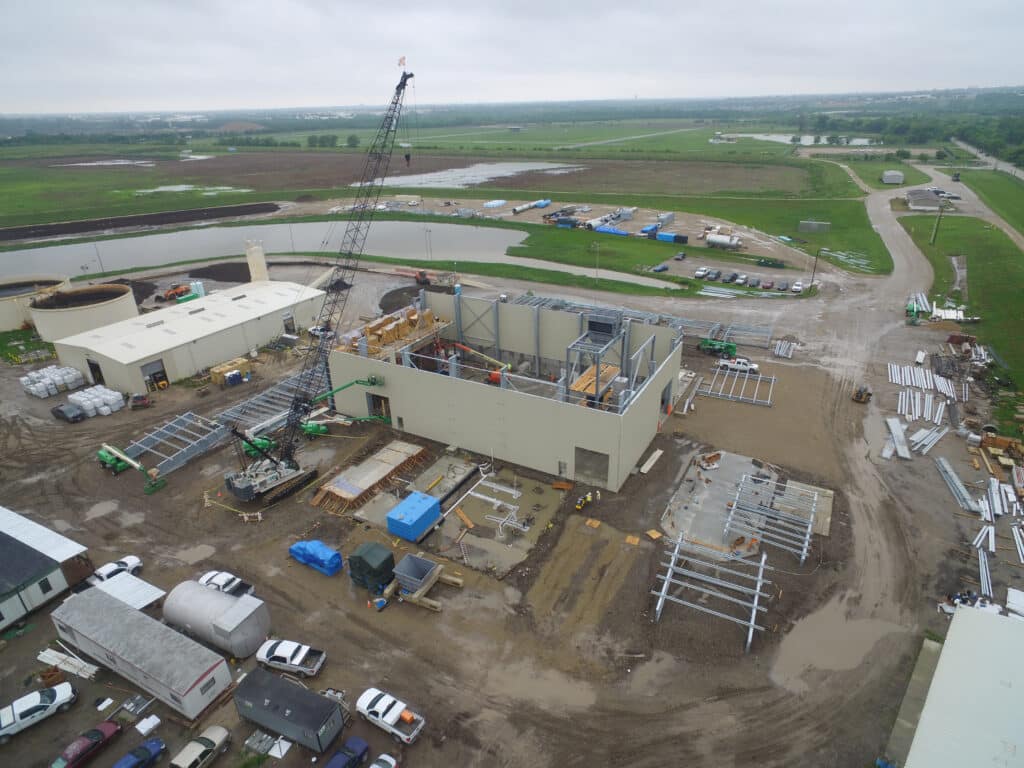
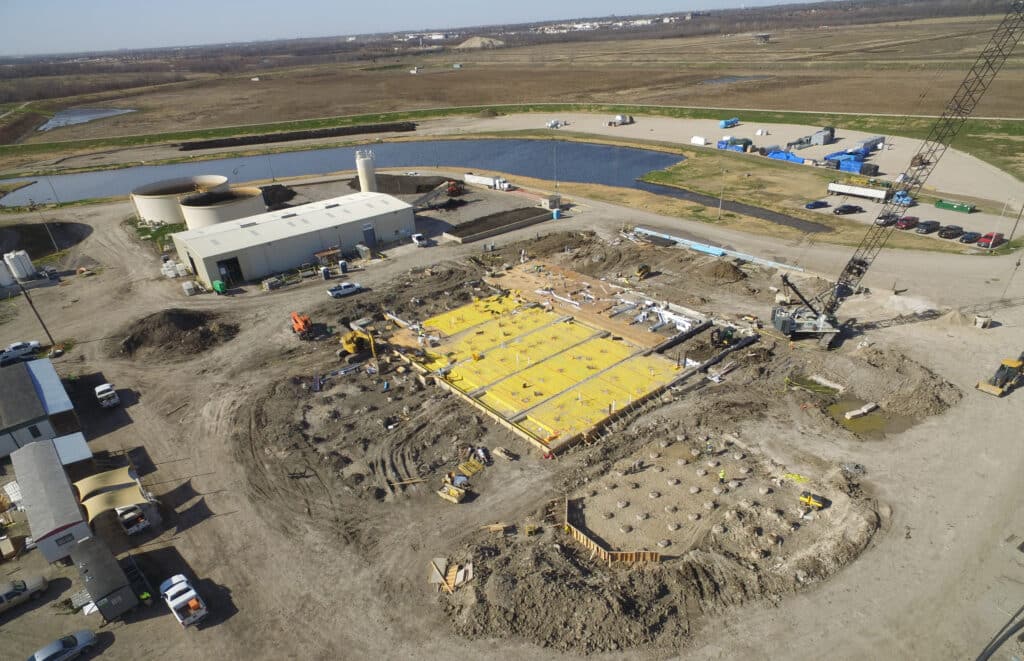
- DBOM Project Delivery Approach: The DBOM delivery approach, the first for the City, allowed the collaboration of all stakeholders throughout the design and construction phases. The Project Team utilized each member’s strengths to provide a DBOM delivery approach that could meet the City’s accelerated schedule of 30 months. Continuous collaboration between the Project Team and the City was required. Accelerated early work packages for piers and foundations, equipment procurement, and equipment staging as they arrived on site in the order of their required installation in such a manner that it was easily identifiable and retrievable were critical to the project’s success.
- Dryer Capacity: The single-train Andritz Drum Drying System provided for the project is the largest rotary drum dryer in the world in a biosolids application. The dryer has a water evaporation capacity of 14 metric tons per hour (30,865lb/hour). Having a single dryer, as opposed to multiple trains, allowed for significant cost savings for the City. The dryer is currently being fueled by natural gas with the added planned capability to accept biogas produced from the Village Creek WRF anaerobic digesters to supplement the natural gas supply.
- Process Water Management: The process water requirement for the Village Creek WRF condenser is 1,100 gallons per minute, representing significant demand and operational costs. To reduce this demand and operating costs, the process water and condensate from the condenser are recirculated in a closed-loop system, reducing the condenser process water demand by about 50 percent. This project was the first time a closed-loop condensate recycle system was implemented for a drum drying system of its kind, saving about 792,000 gallons of water per day.
- Nitrogen Interization: A typical drying system pneumatically conveys the pellets to storage silos with compressed air. To increase the facility’s safety and reduce the potential for fire or explosion, an onsite nitrogen generation system is used to pneumatically convey the pellets from the drying system to the silos. This provides a blanket of inert nitrogen gas over the pellets stored in in the silos. This is the first time an onsite nitrogen generation system has been used to pneumatically convey product to silos.
Sustainable Results
By changing the method of biosolids treatment at the Village Creek WRF, the City is realizing the benefits of forward-thinking and utilizing advanced technology.
- The dryer has sufficient capacity to dry all solids through the year 2040. It can produce up to 110 dry tons per day of end product for beneficial reuse.
- The drum drying system produces granulated Class “A” biosolids that appeal to a wide variety of end users due to their nutrient content, low dust, low odor, durability, uniformity, and size. The final product at the Village Creek WRF is a registered commercial fertilizer that can be spread directly on broad acreage and cash crop operations, used as a bulking agent with fertilizer blenders, bagged directly and sold, or used as a biofuel.
- The beneficial reuse of biosolids reduces waste, recovers natural resources, generates renewable energy, lowers greenhouse gases and improves water quality in our waterways.
- The dried pellets contain less than 10 percent water, and as a result the tonnage of biosolids being hauled to land application sites has been reduced by over 70 percent. The volume of biosolid being trucked from Village Creek WRF has reduced from an average of 22 trucks per day to 6 trucks per day.
- The City’s operating costs for biosolids management have reduced from an average of $410 per dry ton before the project to $310 per dry ton after the project, representing about a 25% reducing in operating costs and resulting in millions of dollars saved annually.
- The City has not had a single odor complaint at land applications sites since the facility came online in July 2022.
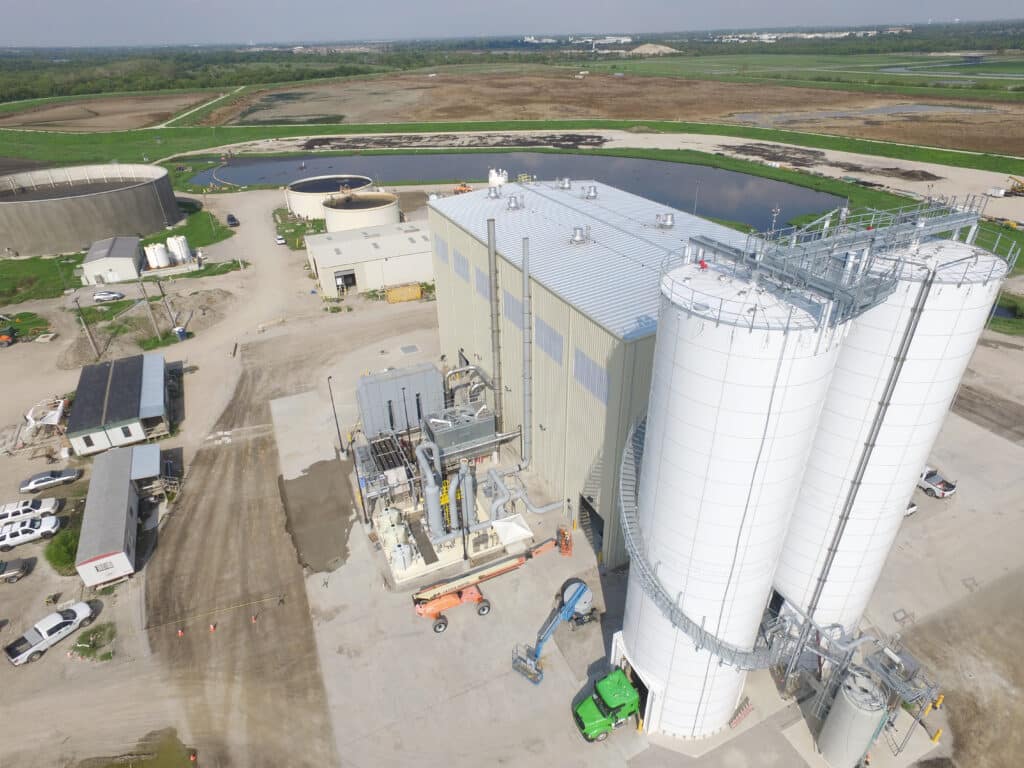